Plant visualization
It houses the following departments:
- book-keeping
- economic & planning
- HR
- logistics & maintenance
- technical inspection
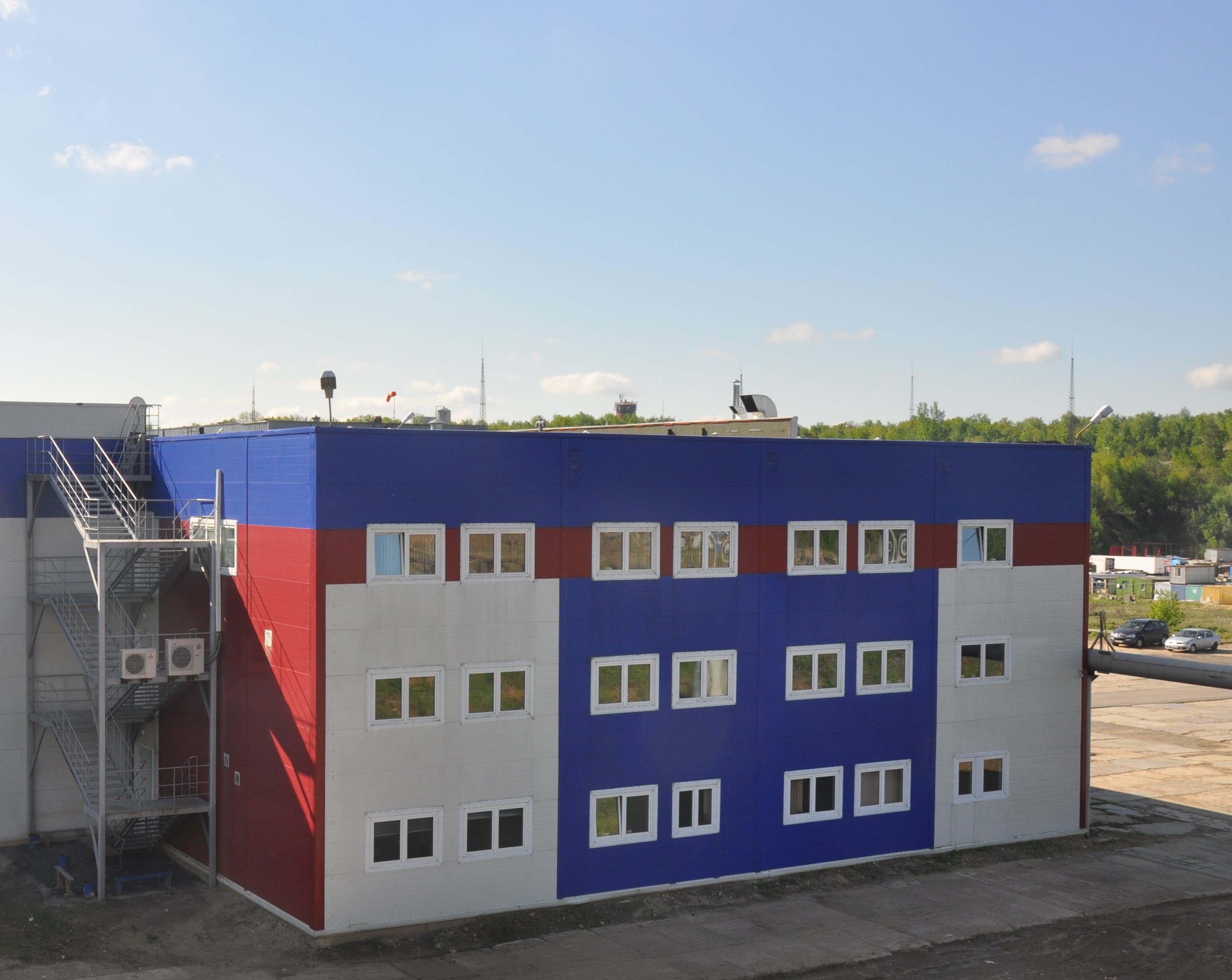
In this area manufactured ball valves are cleaned off grease and dirt, painted and the paint application quality is checked (by measuring the paint layer thickness).
Each area is zoned for packaging and storage of the manufactured products.
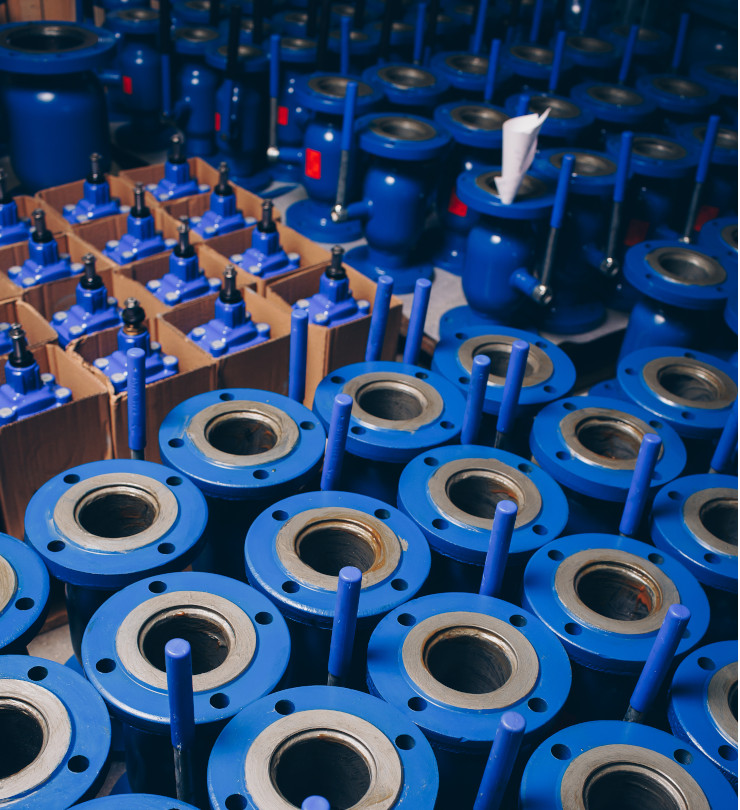
In machining areas, located in workshops No. 1 billets of balls, pipes, body parts are processed using the high-precision machines of the leading international and Russian manufacturers:
- processing centers with numerical software control
- numerical control lathes, universal lathes and milling machines
- horizontal boring machines
- vertical boring machines
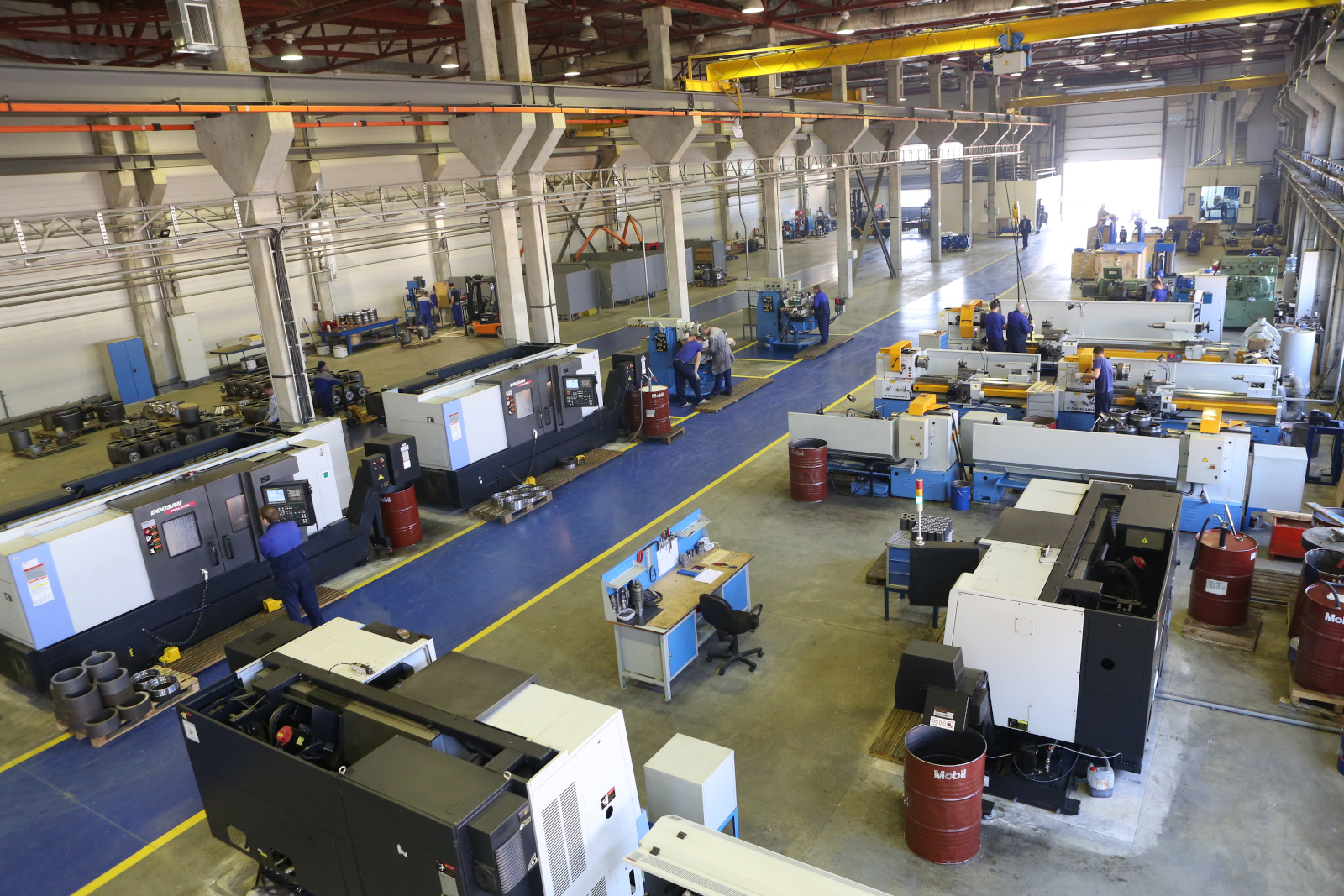
Special equipment is used to crimp bodies of ball valves, die-welding structures and pipe billets. Working force developed by the presses: from 100 to 630 tons.
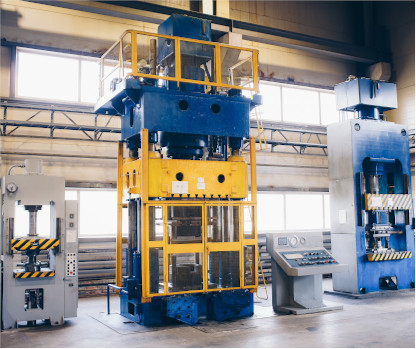
In the preparation area billets for ball valves are cut with automatic band saws UMT (Bulgaria).
The area equipment includes lifting mechanisms, band saws and shot blasting chamber for billets.
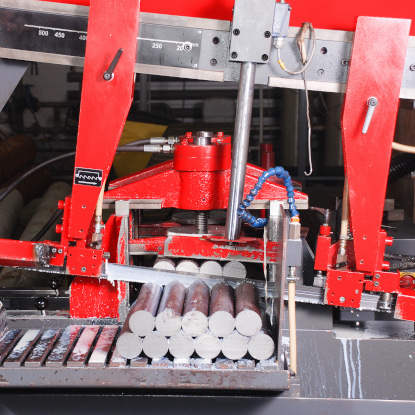
In the UZTPA assembly areas pipeline valves DN 15 to DN 1400 and rubberized wedge gates DN 50 to DN 600 are put together and assembled.
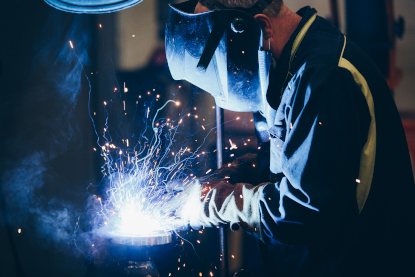
This station is used to weld the ball valve body and stem housing using high quality welding consumables.
Welding station equipment:
- automated welding complex Fronius (Austria)
- automated welding complex PEMA (Finland)
- welding robot PEMA (Finland)
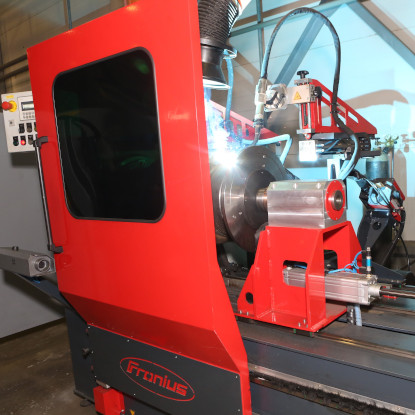
In the test area, welds are tested for strength with water and air. Each ball valve unit is tested, regardless of diameter.
Equipment:
- test bench for testing small-sized valves
- test bench for testing medium-sized valves
- test bench for testing large-diameter valves, VENTIL (Netherlands)
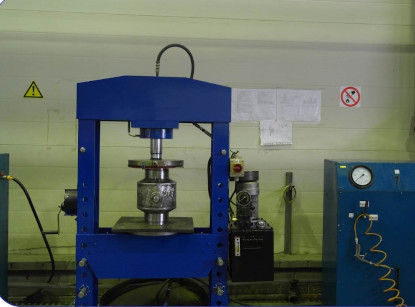
In this assembly area shut-off valves are put together and assembled. All components are delivered to the assembly areas in accordance with the ISO 9001 quality management system and under the control of the Quality Control Department.
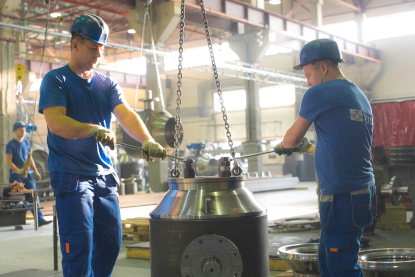
This station is used to weld the ball valve body and stem housing using high quality welding consumables.
Welding station equipment:
- automated welding complex Fronius (Austria)
- automated welding complex PEMA (Finland)
- welding robot PEMA (Finland)
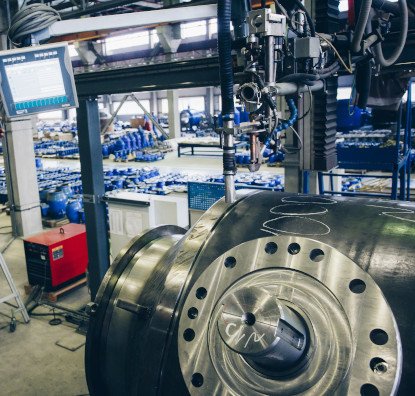
In the test area, welds are tested for strength with water and air. Each ball valve unit is tested, regardless of diameter.
Equipment:
- test bench for testing small-sized valves
- test bench for testing medium-sized valves
- test bench for testing large-diameter valves, VENTIL (Netherlands)
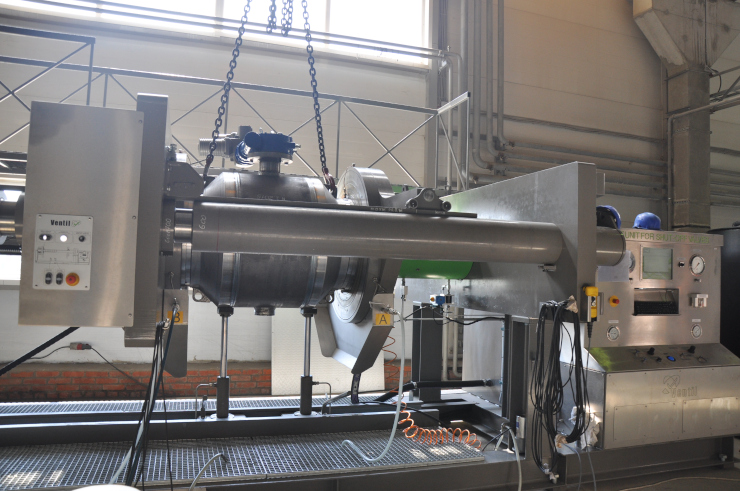
In machining areas, billets of balls, pipes, body parts are processed using the high-precision machines of the leading international and Russian manufacturers:
- processing centers with numerical software control
- numerical control lathes, universal lathes and milling machines
- horizontal boring machines
- vertical boring machines
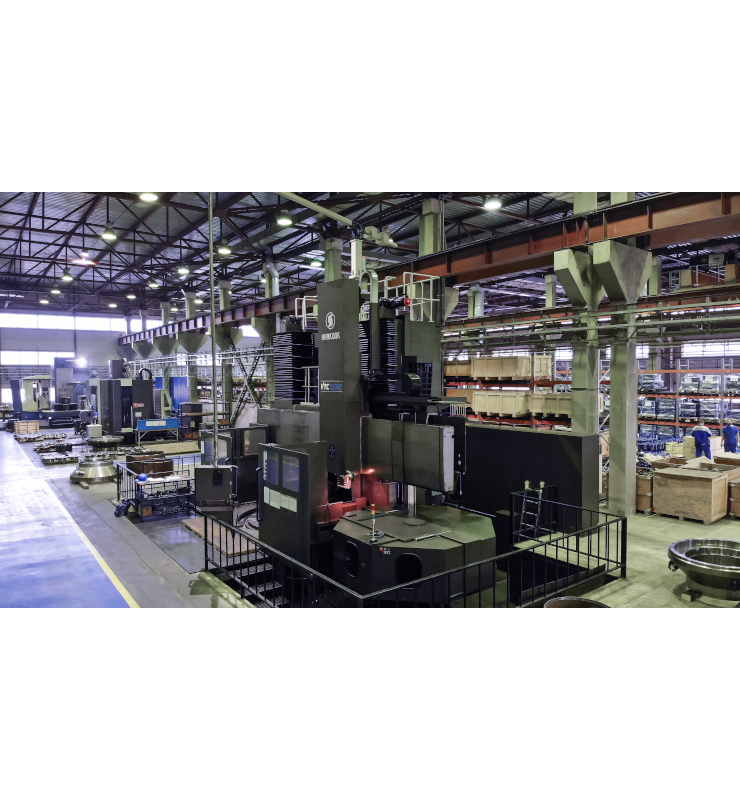
This station is used to weld the ball valve body and stem housing using high quality welding consumables.
Welding station equipment:
- automated welding complex Fronius (Austria)
- automated welding complex PEMA (Finland)
- welding robot PEMA (Finland)
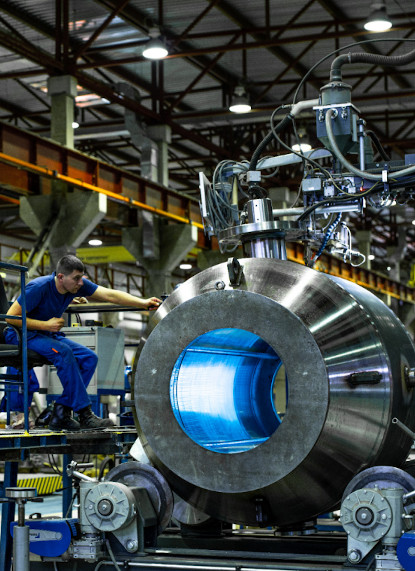
In the test area, welds are tested for strength with water and air. Each ball valve unit is tested, regardless of diameter.
Equipment:
- test bench for testing small-sized valves
- test bench for testing medium-sized valves
- test bench for testing large-diameter valves, VENTIL (Netherlands)
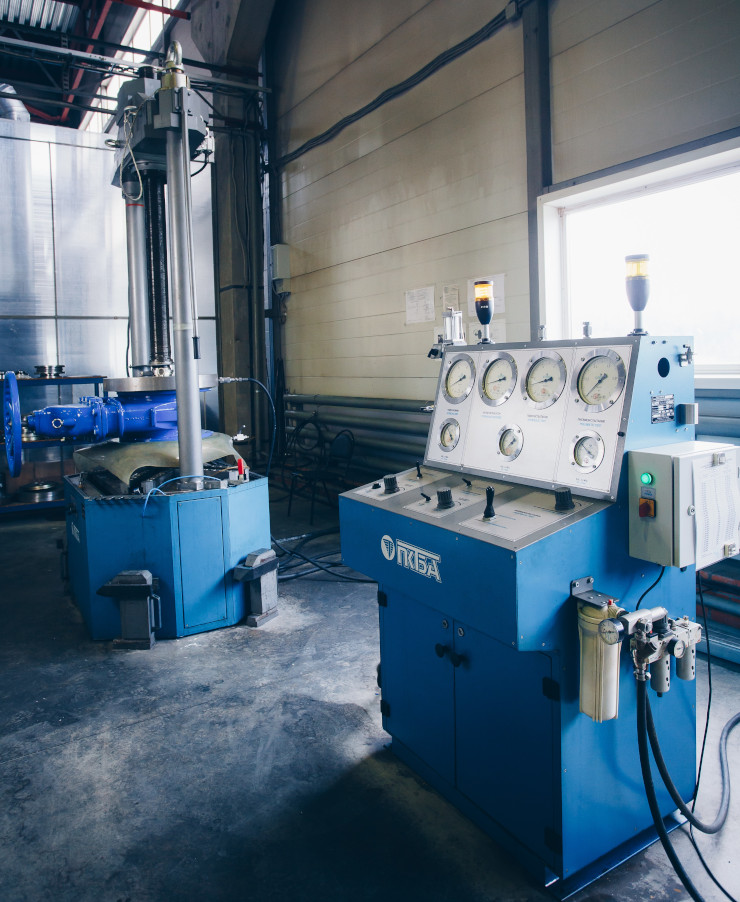
Products are painted with high-temperature two-component epoxy high-filled primer enamel in the TERMOMAX paint chamber.
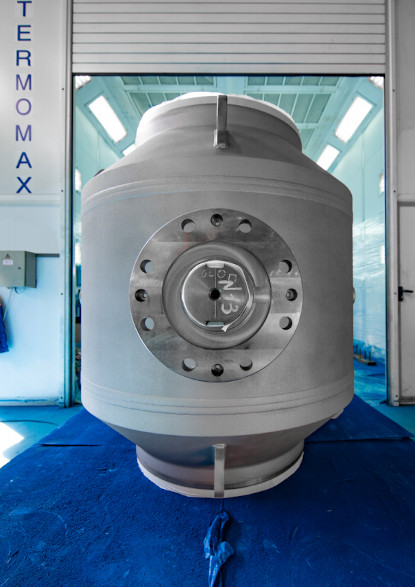
Finished products storage area at the plant proper.
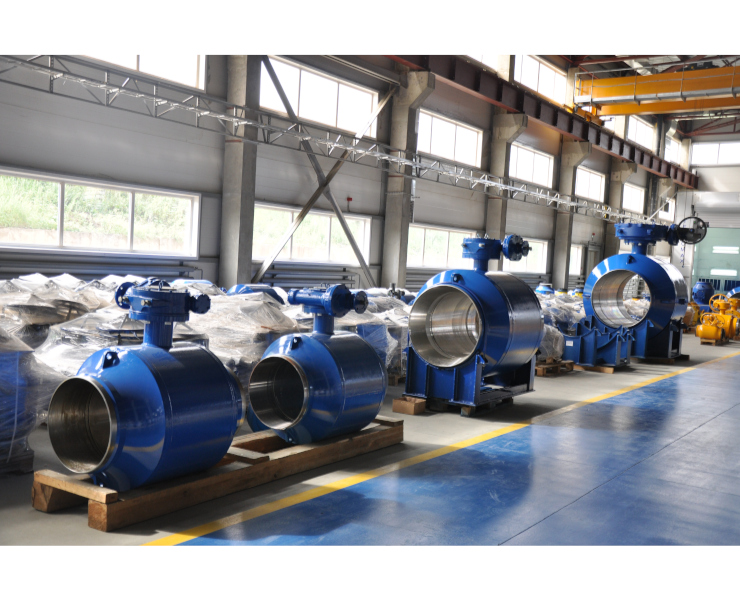
Storage of the accessory materials.
Equipment:
- overhead crane
